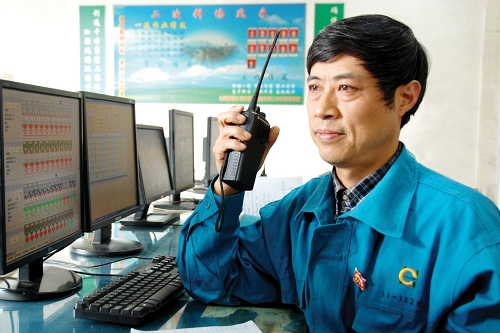
从大山里走出来的国家技术能手 邵宏斌,男,48岁,杭钢集团国家级技能大师工作室组长。初见邵宏斌,个头不高,脸颊削瘦,一双炯炯有神的眼睛到让人印象深刻。淡定而坚毅的眼神,青筋突出的手背,行走如风的脚步,叫人一看便知这是一个勤快、任劳的人。 1987年, 生活在龙游大山深处的邵宏斌,高中毕业。为了挑起家庭的担子,改变一家五口靠父亲做乡村教师微薄收入清贫拮据的生活,与村里的几个同龄人一起筹办起造纸厂。这时,杭钢正巧到龙游招工,一直想去大山外面看看的邵宏斌,毅然选择了杭钢,做了一名最普通的皮带操作工。 皮带运输技术那时在国内还不普及,故障发生率高,他所在岗位上的皮带由于长度长,电机马力不够,再加上是斜坡皮带,经常发生倒料现象,不仅影响生产,更浪费人力。很多人都觉得要解决这个难题,必须对皮带动大手术,邵宏斌在经过一段时间的摸索,提出了“利用旧皮带做刹车装置防止倒退”的合理化建议,一个小改革就解决了大难题。 工作之余邵宏斌常常窝在钳工组里,因为那里能学到更多的东西。他给钳工组师傅们打打下手,不懂就问长问短,渐渐地钳工师傅们都喜欢上了这个爱问问题的小伙子,把他当成了钳工组的编外人员,都愿意把自己的技术和经验倾囊相授。由于动手能力强、脑子灵光又能吃苦,第二年邵宏斌就被调到了钳工组,从普通工人成为了一名技术工人。这下他的工作热情就更高了,他整天跟在师傅后面,有活都抢着干。当时班组里最苦的活就是维修热筛和轴流冷却风机,这两样活都归邵宏斌和师傅包干。轴流冷却风机建在半密封的烟道里,里面空间狭小,温度超过60℃,油管和密封圈松动漏油后,邵宏斌就要爬到里面维修。维修平台在风机下方,必须仰起头才能换密封圈、拧螺丝。每次维修时,滴滴答答的油混着灰尘下雨似地往他身上洒,不一会儿,他就成了油人、泥人。每干一趟活,邵宏斌都要把自己“扔”在澡堂子里让同事用香皂、工人洗手液使劲地搓上好几个小时。 邵宏斌在钳工组一做就是6年。这6年,他如鱼得水,全身心对投入,车间所有机器设备的规格、型号、脾气几乎被他摸了个透,用邵宏斌的话说就是吃苦“吃”出了一身本事。这一身本事为他今后的成功打下了基础。 1994年,他调到烧结值班室,由于他能琢磨、善总结,很快就成了值班室技术最好的人。他的脑袋就像计算机一样,只要看到配料单和各种料的数量、成分,就能准确地推断出成品的各项指标。因此,当烧结矿质量出现波动时,同事们都喜欢向他请教。2005年,1号、2号烧结机上马,新任值班室组长邵宏斌雄心勃勃,力争开拓新局面。但是现实和理想的差距是巨大的,新设备、新工艺、新员工、新的操作方法,一切都是新的,老师傅碰上了一大堆新问题,尤其是烧结点火不均匀、固体燃料消耗高、产质量的潜能不能充分发挥,这三大问题都急需邵宏斌去解决。 邵宏斌从总结数据入手,理清各种关系,不断创新操作方法。经过半年多的攻关,他提出了“90平方米烧结机点火和厚料层先进操作法”,彻底解决了烧结点火不均匀、产质量不高和固体燃料消耗大的“症结”。这一操作法在三台烧结机推广应用后,每年可产生效益数百万元,得到上级评审部门的肯定,被评为浙江省先进职业操作法,并以他个人名字命名。 烧结生产过程中,大量含水、温度高、成分复杂的粉尘在灰斗内凝结成大块堵住电除尘灰斗,造成排灰不畅,影响烧结生产。每次堵料后,都需要有人爬进灰斗清灰。灰斗内是个高温、高尘、半密闭的空间,人进去前浑身清爽干净,干完活后爬出来,除了眼睛部位被风镜保护着,其他地方黑得连衣服的本色都无法辨别,细微的灰尘还钻进了毛孔,洗澡的时候只有用洗衣服的刷子把全身刷得通红才能洗干净。 “不行,这样的情况必须要改变。”邵宏斌暗暗地给自己下任务。经过摸索和多次进灰斗亲身体验,邵宏斌发现灰斗停机后不及时关风门震打,那么吸附在电除尘阳极板和阴极丝上的灰就容易粘结成块。找到原因后,邵宏斌积极寻找对策。2008年初,他提出了“减少烧结机机头电除尘灰斗结块的先进操作法”。实施后,情况大为改观,灰斗堵料现象锐减,设备作业率提高了2.13个百分点,该先进操作法获得了集团公司一等奖。 在不断的生产实践中,邵宏斌还先后提炼总结出“电子皮带秤匀速配料”、“合理控制烧结机机上烧结矿结大块”、“烧结混合料提前预热”等十多项先进操作法和近百条合理化建议。 2011年下半年,炼铁厂成立高技能人才创新工作室,邵宏斌被任命为工作室带头人。当时,炼铁厂正在大量使用低价矿,低价矿水分大、粘性高、成分杂,无法用以往的方法进行生产。为此,邵宏斌带领工作室成员深入进行课题攻关,他提出了利用高炉返矿较好的干燥性和流动性特点,将高炉返矿与印尼粉按5:3的比例混匀后再进受料槽,在预配料中配出使用的合理化建议,一举消除了弊端。同时,他又提出了“如何在使用粒度过粗的混匀矿后烧结过程透气性过剩影响烧结矿产质量” 的攻关课题。,通过不断试验,他将混匀矿水分由原来的7.8%±0.2降低到7.6%±0.2,同时采取了厚料层烧结方法,一举破解了难题,实现了烧结料层稳定,使烧结矿转鼓提高1~2.5个百分点,单单这一项每年就可降低生产成本258.84万元。在近几年中,他还先后总结出了提高皮带供料作业率,为直供料提供时间保障、将白云石粉从一次料场直供到烧结机配料仓,降低短驳运输成本、180㎡烧结机稳定均衡内循环返矿比例技术攻关、混匀矿头尾料回堆,解决头尾料对烧结生产的不利影响等共28项困扰烧结生产的难题,为企业节约原料成本3.37亿元。 2005年以来,炼铁厂先后提出了“生产稳定高效、资源充分利用、安全环保正常、员工幸福安康”以及打造“花园式工厂”等目标。邵宏斌积极响应铁厂号召,在技术攻关中竭尽全力寻找效益和环保的平衡点。 2012年5月,炼铁厂为了降低烧结固体燃料成本,采用部分煤粉来替代进口焦粉,而煤粉较湿粘,对运输和破碎是个难题,传统的解决办法需要投入上百万的费用。邵宏斌经过的探索,大胆的提出了“煤焦混合放料破碎”的方法,将粘湿的煤粉和干燥的焦粉混匀后再用破碎机进行破碎。经过试验,采用此方法不仅减少了大量焦粉的使用,降低了炼焦产生的能源消耗和系列环保问题,推进了“花园式工厂”的建设,以煤代焦也大大的降低烧结工序成本。 另外,邵宏斌针对烧结点火不均匀,固体燃料消耗高等结症,收集了大量的数据,经过分析后发现问题所在,并在实际生产中不断进行摸索,不断进行创新操作方法,以稳定24小时配料量为前提,最终提炼出了《90平米烧结机点火和厚料层先进操作法》,推广运用后效果非常明显,彻底解决了烧结点火不均匀和固体燃料消耗高的结症,使烧结固体燃料消耗逐步降低,生产能耗显著下降,吨矿固体燃耗降低9.2kg,工序能耗降低6.82kg/t,每年节能降耗数百万元。 “要当一名称职的工人,既要会干活,更要会总结。”邵宏斌这样说的,也是这样做的。从1987年进厂,先后在杭钢集团公司炼铁厂28平米烧结值班室、烧结维修钳工组、105平米烧结值班室等岗位工作,任劳任怨,积极开拓创新,为杭钢集团降本增效做出了巨大的贡献。他先后获得杭钢集团公司劳动模范、浙江省劳动模范、全国技术能手等荣誉称号,2012年获得钱江技能大奖、全国五一劳动奖章、2014年度入选享受政府特殊津贴人员等。 |